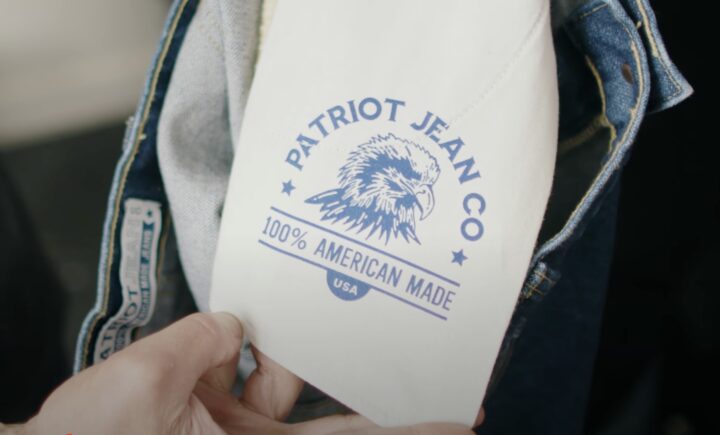
Whether you’re a man or woman, you know jeans have changed considerably over the decades. No longer made of rugged blue cotton denim (aka dungarees), jeans come in all kinds of colors and often include Lycra in order to accommodate different body types and shapes – and reduce costs.
Plus, you have the various styles: skinny, boot cut, wide, flare, etc. Personally, I find jean shopping exhausting. Nothing fits. I hate skinny-stretch and the thin cheaply made material. The one woman’s brand I used to love, Not Your Daughter’s Jeans, moved production from the US to China and ruined the brand known for its fit and quality.
Today, I wear jeans from various manufacturers: LL Bean (they carry the 207 Vintage non-stretch line but not made here), MOTHER Denim (made here of imported stretchy material), and Cabi (completely offshored).
I keep asking, “Can’t anyone make normal old jeans that fit, feel good, and are made in the USA with US-sourced denim?”
“I had the same revelation,” says Patrick Mate, founder and CEO of Patriot Jean Co. An Army veteran, Mate worked for an Aerospace company at the executive level and wore suits.
“Then, COVID hit, and I still wore a sports coat and dress shirt for Zoom calls, but realized I could wear jeans. I searched for a great pair of jeans that were made in the US, and that’s when I realized the depth of the problem.”
From “clueless” to an LLC
Over 450 million pairs of jeans are sold in the USA every year – with only 3% made in the USA. Or, if the jeans are made in the US (such as the MOTHER Denim brand), they’re made of material sourced from overseas.
“The market is quite large,” says Mate. “I also realized people like me are willing to pay extra for Made in USA. The fact that 3% of jeans are made here told me it could be done.”
After putting together a business plan, he talked to a few people, including Dean Bundschu, a leader and advisor in the veteran entrepreneur space, and Mate’s old college ROTC buddy. After five minutes listening to Mate’s presentation, Bundschu said, “Go for it. What’s the worst that can happen?”
He also connected Mate with fellow Army veteran and entrepreneur Dean Wegner, founder and CEO of Authentically American Apparel (also interviewed for this blog, see all links below).
“Dean has given me his time and contacts list and has been tremendously helpful,” says Mate.
After reaching out to colleges and universities for interns who could help him, Mate was introduced to the White Oak Legacy Foundation (W.O.L.F.) in Greensboro, NC.
W.O.L.F. – Dedicated to denim history
Denim consists of two ingredients: cotton and indigo dye, which is insoluble and sits on top of the cotton. This is why your beloved denim jeans have wear patterns. Due to wear and stress, the indigo chips off. (All denim facts from the W.O.L.F. website.)
Peoples all over the world figured out a way to make indigo dye hundreds of years ago (for example, Britain used woad-based pigment for blue dyes), but it wasn’t until Adolf Von Baeyer, a German chemist, figured out how to make a synthetic indigo molecule in 1870, that things changed significantly. Now, indigo could be made in large quantities for textile manufacturing; in 1895, British India exported 9,000 tons of indigo.
The dying process, however, was rife with inefficiencies. In 1921, the Touchstone process solved many of the challenges with uneven dyeing. It also significantly streamlined the manufacturing process. Today, dye masters control the consistency of the dye through sight, touch, and even smell.
In addition to preserving denim history, W.O.L.F. offers Denim 101 classes several times a year. When Mate called to register, he was told the next class was already filled, but a week later, he learned someone backed out – which opened a slot for him.
“That class was amazing,” he says. “We visited yarn spinning mills and a denim production mill, and we learned the technical components of making denim. My classmates were people from all the major denim companies – and here I was, a company of one. Everyone was very nice – it was a great opportunity for networking.”
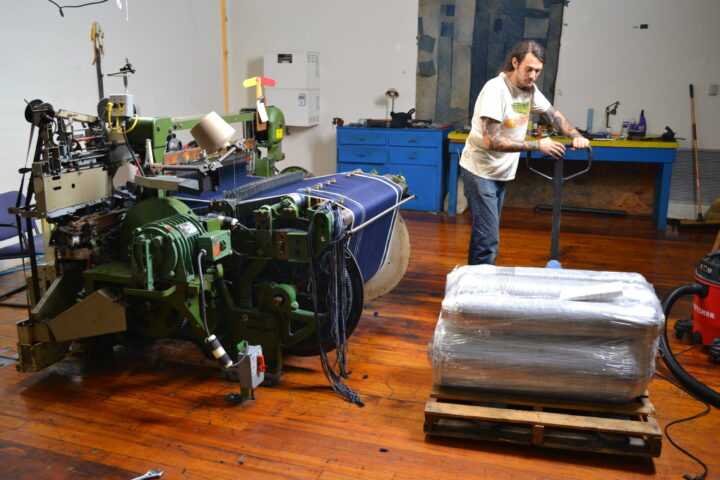
W.O.L.F. also operates a for-profit subsidiary, Proximity Manufacturing Co., which manufactures limited runs of denim using traditional equipment, such as modified Draper looms.
According to the website, these shuttle looms were originally built by Draper Corporation, a Hopedale, Massachusetts-based textile equipment manufacturer, sometime during the 20th century, and spent the last several decades inhabiting the wooden floors in the Cone Mills White Oak Plant (now closed).
Proximity also hired many of the former Cone employees with decades of experience who now oversee denim production. (Link below.)
The production cycle: from field to construction
All Patriot Jean Co denim jeans are made of cotton grown in the southeast United States. The cotton is harvested, graded, and then shipped to a yarning mill – where it’s put on large spools and then sent to the dye house. Dyed yarn is finally sent to the denim mill house – in huge yardages.
According to Mate, North Carolina was the center for denim manufacturing – millions of pairs of jeans were produced every month. Due to NAFTA and the cheapness of foreign labor, denim mills began closing and moving overseas.
Established in 1845, and the first cotton mill in Northwest, GA, Mount Vernon Mills, Inc. is still producing textiles today – including denim at its Trion, Georgia facility. It’s the largest denim manufacturing plant in the United States.
Side note: Selvedge and weave
“Patriot Jean Co denim jeans are made of high quality ring spun yarn – this means the strands are longer and stronger, and much softer,” says Mate.
His comment prompted me to ask: “What is selvedge denim?” Like many people, I knew about the 2017 closing of Cone Mills’ White Oak Plant, “the last American selvedge denim mill,” according to Heddels, a news and education website.
Selvedge denim refers to fabric that’s shuttle-loomed, a traditional method of weaving. Due to this process, the edges of the loomed cloth have a nice finished edge, noted in the photo below — the seam edge is white with the red thread running through.
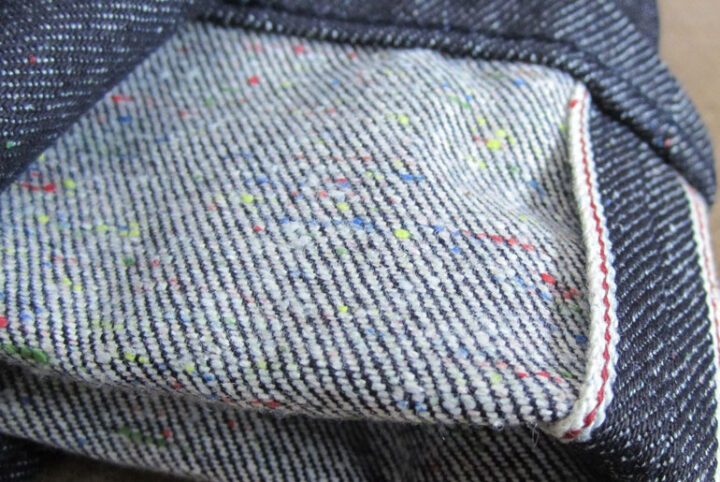
Regular non-selvedge denim has the common overlock edging to keep the material edges from fraying.
According to Heddels, “weave refers to denim weight — 3×1, 2×1, and 1×1 or plain weave — or the number of warp threads versus weft threads. 3×1 is the most common in selvedge denim, chiefly because any denim over a 10.5 oz. per square yard weight is 3×1.”
While doing my research for this post, I pulled out the jeans I had custom-made ca. 2018. I had been told the material came from one of the last Cone Mills runs, so I assumed they had a selvedge edge. Alas, they do not. But the denim is wonderful — and as you can see from the seam, a lovely deep indigo blue.
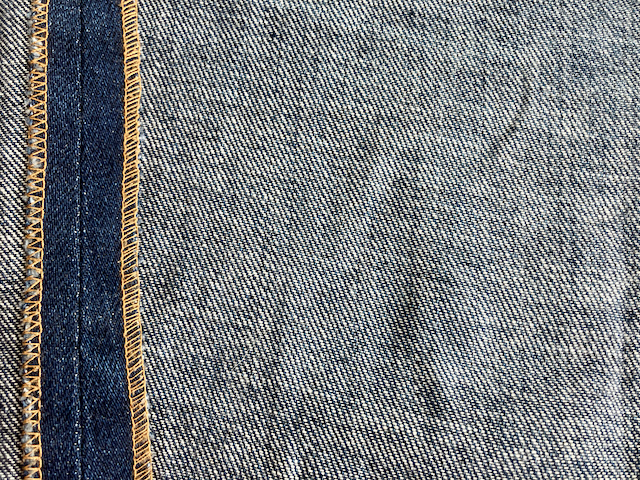
“What you have there,” said Mate, “is a 3×1 right-hand twill. Definitely not selvedge, but they still could have come from an old Cone Mills batch, or were produced by Mount Vernon Mills or Vidalia Mills. I am unsure.”
For his jeans, Mate chose a more unique weave called “broken twill.” According to Mate, big brand jeans, such as Lee’s or Levi’s, use a traditional weave that results in the diagonal pattern seen in the selvedge photo above.
With the “broken twill” weave, the pattern is interrupted at regular intervals, which gives Patriot Jean Co denim jeans a distinctive look and character.
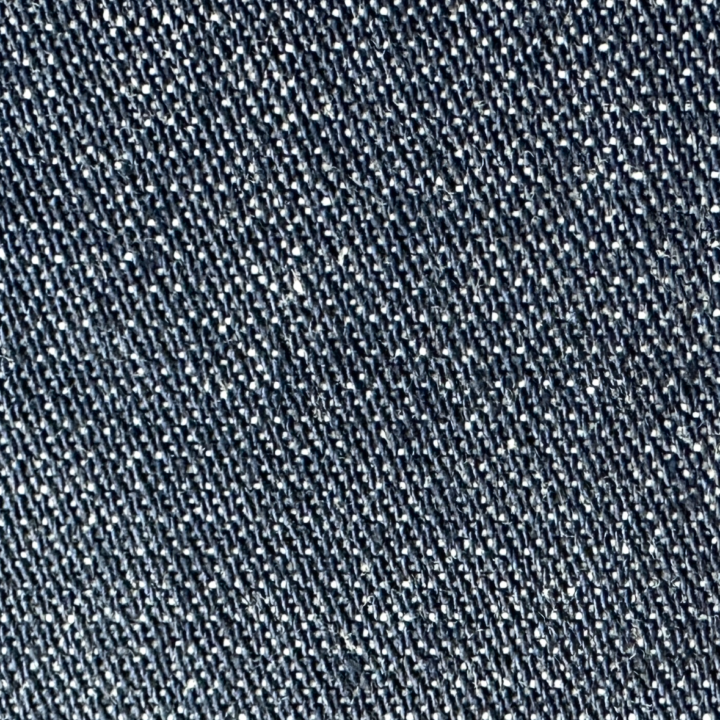
“If you watch the TV show Yellowstone, you’ll see it. The characters wear broken twill denim,” he says.
Patriot Jean Co denim jeans are made with heavy 14.75 oz denim, a throwback to 1980s jeans; this rugged material holds its shape and forms to your body. To maintain fit, Mate advises you not wash your jeans unless they stink or have heavy dirt.
Committed to Made in USA
Mate’s target audience is men, ages 30 – 60, who appreciate a higher-end jean that also happens to be made in the United States. He offers two styles and one wash, but plans on introducing new styles in the coming year.
And no, he won’t be making women’s jeans. At least not this year.
“Everything about our jeans is made in the US,” says Mate, “including the tags and buttons. It was nearly impossible to find made in US buttons, but I found a company who had shipped their machines to Mexico and Asia. They shipped the equipment back and now make our buttons and rivets.”
In our follow up emails, Mate wrote: “Even into the 90’s and 00’s, up until Cone Mills and a few last mills gave up U.S. operations, big brands (Lee, Levi, Wrangler) would source their denim from a U.S. mill and then send the denim to a cut-and-sew facility in the U.S. – a large number of these facilities were located in El Paso, Texas.
“I’ve been through a couple of these once mighty factories that are now either closed, scrambling to stay in existence, shifted operations out of the country, or now produce uniforms for the military.
“Unfortunately, it takes about 6 months of good labor to really become efficient at cutting-and-sewing denim, so the U.S. has lost quite a bit of workforce.”
Mate cites the positive aspects of manufacturing in the United States, such as bringing jobs back to the U.S., supporting existing mills and suppliers, and keeping production local – which also reduces the environmental impact.
Get the Keep It Made USA newsletter.
Twice monthly; zero spam.
Links
Patriot Jean Co — Support your fellow American workers by purchasing Made in USA denim jeans at the company website
Dean Bundschu — LinkedIn
Dean Wegner, Founder and CEO, Authentically American Apparel — Keep It Made USA write up
White Oak Legacy Foundation (W.O.L.F.) — Website
“Know Your Twills – 3×1, 2×1, and Plain Weave” — Heddels
Proximity Manufacturing Company — A for-profit subsidiary of W.O.L.F.
Full Disclosure
I’m not paid nor asked to write about products or the companies that make them. All links in this piece are FREE — meaning, they’re not sponsored or paid for.
My mission is to keep manufacturing jobs stateside and this blog is my way of giving back. We like to think a “small” choice, such as purchasing something made in the US, won’t make a difference. It does.
Rick Horton
Awesome read. American denim come on back!
Dianna Huff
Thank you, Rick — and yes, very exciting!