“My father never said I couldn’t pursue a manufacturing career because of my gender,” says Mary Planeta Fitzgerald, President of Acme Wire Products. “I never had the mindset that manufacturing was off-limits.”
It’s this positive mindset that has served Mary and her siblings, Michael Planeta and Edward Planeta, Jr., well in the years they’ve been running the company, a second-generation family-owned business in Mystic, CT. Collectively, the sibling team has 70 years of professional experience actively running Acme Wire Products.
Acme Wire Products creates custom wire products such as lacrosse face masks or wire cages, wire baskets for the automation, food and medical industries, metal guards of all types, CNC wire forms, and even sometimes “mystery” components whose use is classified.
Acme Wire Products was started in 1970 by Edward Planeta Sr., whose vision was to become the premier wire company in the U.S. Although Mary had worked on the production floor to earn some extra money while in high school, once she graduated from college, she began looking for a job in industrial sales rather than go to work for her dad.
“My first job was with a company that made shaped wire,” Mary says. “I knew how to run a computer system and was hired for that position and shortly thereafter transitioned to sales. It was a very male dominated field and my co-workers didn’t quite know how to deal with an eager young woman with a passion for manufacturing. A few years later, I called my dad and said I wanted to work for him. I started out in marketing administration, learned the company operations from the ground up, and eventually assumed responsibility for the entire sales and marketing function.”
Her brothers followed. Michael, who was working for Arthur Anderson as a management consultant, joined the team five years later. It took Edward Jr. another ten years; he was in the restaurant business and transitioned to manufacturing because he wanted a more traditional schedule. “With our backgrounds, we all bring different skills to the table,” says Mary.
Advisory Board helps Acme Wire go to a whole new level
In 1999, because of the exposure to other family businesses within the UConn Family Business Program, the family added an outside advisory board. This board, according to Mary, helped the three siblings make the transition when they purchased the company from their father. It also helped them determine the roles each would play in running the company.
“The advisory board helped us work out the issues of trust, goals and shared vision,” she says. “We learned how to communicate with each other as well as create documented systems so that we could do each other’s job if necessary.”
The advisory board also helped Mary and her brothers take the business to a whole new level. The siblings streamlined operations and added automation. They became very clear on the types of projects they would take on. Says Mary, “If a project isn’t a good fit for us, or we don’t have the capability, we’ll refer the project to another company, even if it’s a competitor.”
Having documented procedures ensured that Michael and Edward could run the company when Mary took maternity leave — four times!
When asked how she raised four children and ran a company, she laughs. “First, I learned how to delegate!” But in all seriousness, it was the birth of her children that gave Mary and her brothers the impetus to put the documented processes in place that stand them in good stead today.
“I did take three months of maternity leave with each child, and then I brought each one to the office,” she says. “During each leave, my brothers ran the company. Documenting our processes and refining them made me and my brothers better business people.”
Educating the next generation
Mary is a passionate advocate for educating high school students about careers in manufacturing. Currently she’s part of the Eastern Advanced Manufacturing Alliance (EAMA), a non-profit partnership comprised of manufacturing companies in Connecticut and the Quinebaug Valley Community College, the H.H. Ellis Technical High School, and the Three Rivers Community College.
EAMA’s mission is to prepare students and employees to work in the manufacturing industry. Currently, the group is working on a video challenge, “What’s So Cool about Manufacturing?”
“We paired the high school kids with manufacturers in the area,” says Mary, “and now they have to create videos about their companies. It’s a lot of work but I think it will yield good benefits.” The manufacturers’ stories will be told from the students’ point of view with the focus on the exciting career opportunities available within advanced manufacturing.
“We’ve also held open houses,” she adds, “and have invited students to tour Acme Wire.” The tours are open to students and families as a way to educate both on the careers available within the industry. “Our main challenge,” says Mary, “is getting schools to be open to and accepting of our invitations. Our goal is to showcase advanced manufacturing as a primary career focus, not one that is the last resort.”
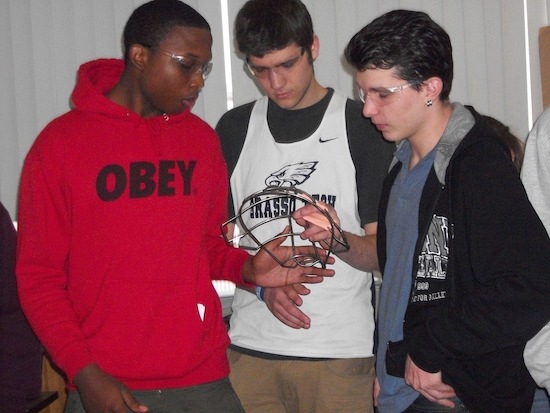
Despite the challenges and the extra work, the outreach is paying off. According to Mary, students are enrolling in pre-manufacturing classes at the two community colleges and are being recruited for jobs at competitive wages upon completion of the programs.
“Although manufacturing is different from when I was growing up and watching my dad run the company, some things have not changed,” says Mary. The company is still focused on offering specialized service to its customers and creating long-lasting relationships.
These values extend outward to the company’s employees, some of whom have been with Acme Wire for decades, and into the community as well. It’s these values that contribute to Acme Wire’s continued success.